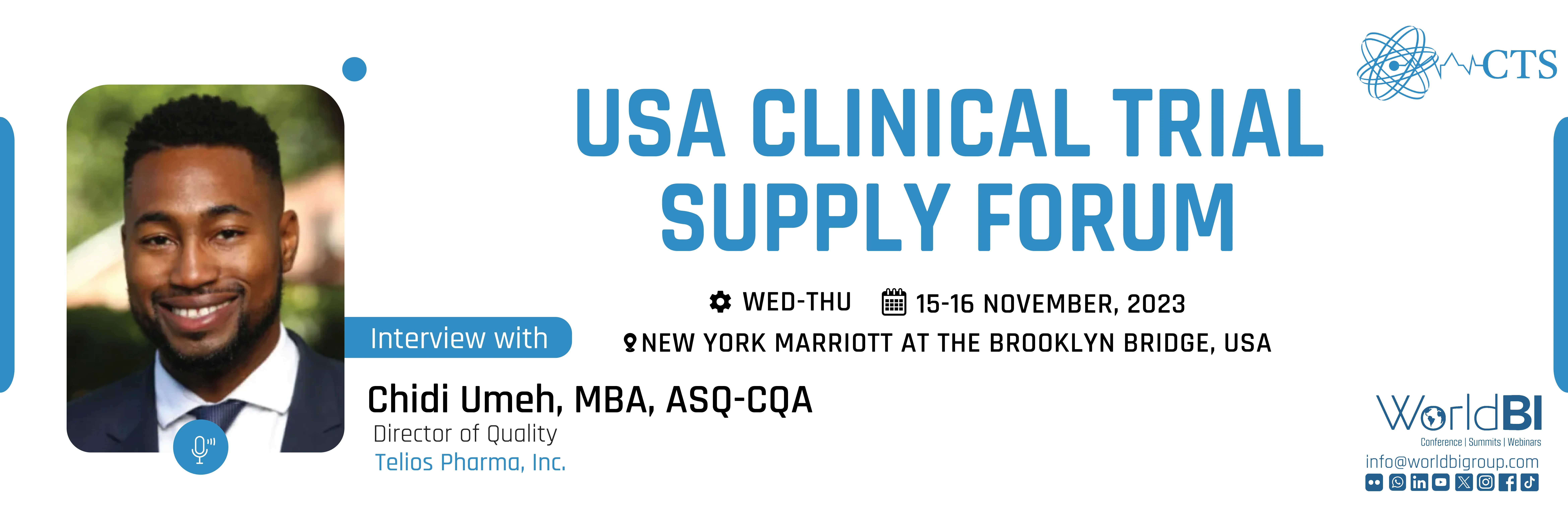
Q1. To get things started, tell us something about you?
I have a double major in Biology and Chemistry. I have been in the industry for 19 years, with various roles including QC Chemist (in commercial manufacturing and contract labs), Supplier Quality Management, and currently in Quality Management in the clinical phase pharma.
Q2. You mentioned your open door policy and individualized management style. What effects do you think this approach has on team performance and growth, and how do you adjust your management style to the particular requirements and talents of your team members?
I am all about approachability. I believe every individual has their strengths and it is up to the manager to bring it out of them. The open door policy allows that so you have constant communication with your team. By keeping the doors open, you can give low performing employees access to you to help with performance improvement, and you give the high performing employees the autonomy to continue as they see fit and reach out when required. The open door also helps the manager keep a pulse on the group and interject where they see fit.
Q3. Cross functional teams frequently collaborate closely with competent individuals. Can you give an example of a particularly fruitful partnership that highlights the importance of good ties between quality and other organizational departments?
As a quality professional, you are the gatekeeper of your products till they get out of the door, so the whole company is dependent on you to be thorough and timely. One of the groups I work with constantly is the Supply Chain team. With close collaboration with supply chain, you also instill quality mindsets in the group. This really helps with communication with suppliers because supply chain teams with quality mindsets are great at holding supplies accountable for quality mishaps, without the constant interjection of quality. It helps streamline the routes of communication between sponsors and suppliers.
Q4. Compliance and auditing are involved in quality assurance. Could you elaborate on your experience with internal, external, and FDA audit preparation and management?
I have worked in commercial manufacturing and contract laboratories, and I currently work in clinical phase manufacturing.
- Internal audits are the most scrutinous because we are forced to take a hard look at ourselves (as we know where the skeletons are buried). There is usually tension between quality and the rest of the company during this audit, but an understanding of us finding and fixing the problem before an outside entity finds the problem is always best.
- External/supplier audits or audits from customers help keep everyone in line. Suppliers are an extension of your facility, so once you make that know, audits are usually smooth sailing.
- For surprise FDA/ for cause audits, having an audit team that is well versed in regulations is key. Having assigned roles to all team members help audits go well. Again, establishing an audit as a collaborative activity between auditor and auditee really helps the audit process.
Q5. What tactics do you use to guarantee compliance and a positive audit outcome?
As mentioned above, letting everyone know that an audit should be a collaborative activity where everyone gets better in the process is key to a successful audit.